プラスチック自動グラニュレーター
本体の プラスチックグラニュレーター 押出機であり、押出システム、伝送システム、加熱および冷却システムで構成されています。
1. 押出成形システム:押出成形システムは、スクリュー、バレル、ホッパー、機械ヘッド、そして金型を含みます。プラスチックは押出成形システムによって均一な溶融物にプラスチック化され、プロセスで確立された圧力の下でスクリューによって連続的に供給されます。押出機ヘッド。
2. 伝送システム:伝送システムの機能は、スクリューを駆動することです。押出プロセス中の供給スクリューの回転速度は、通常、モーター、減速機、およびベアリングで構成されています。
3. 加熱および冷却装置:加熱と冷却は、プラスチック押出プロセスに必要な条件です。
プラスチックペレット化装置 補助機器
プラスチックペレット製造機の補助機械は主に、供給装置、整形装置、予熱装置、冷却装置、牽引装置、計量装置、スパークテスト機、ワイヤー巻き取り装置を含みます。押出ユニットの使用は、オプションの補助機器によって異なります。例えば、カッター、ブロワー、印刷装置などもあります。
矯正装置:
プラスチック押出し廃棄物の一般的なタイプの1つは偏心であり、さまざまなタイプのワイヤーコアの曲がりは絶縁の偏心の重要な原因の1つです。シース押出しでは、ジャケットの表面の傷もコアの曲がりによって引き起こされることがよくあります。主な整形装置のタイプは次のとおりです:ドラム型(水平型と垂直型に分かれる);プーリー型(単一プーリーとプーリーグループに分かれる);ウインチ型は、引っ張り、整形、安定した張力を組み合わせたもの;圧力ローラー型(水平型と垂直型に分かれる)。
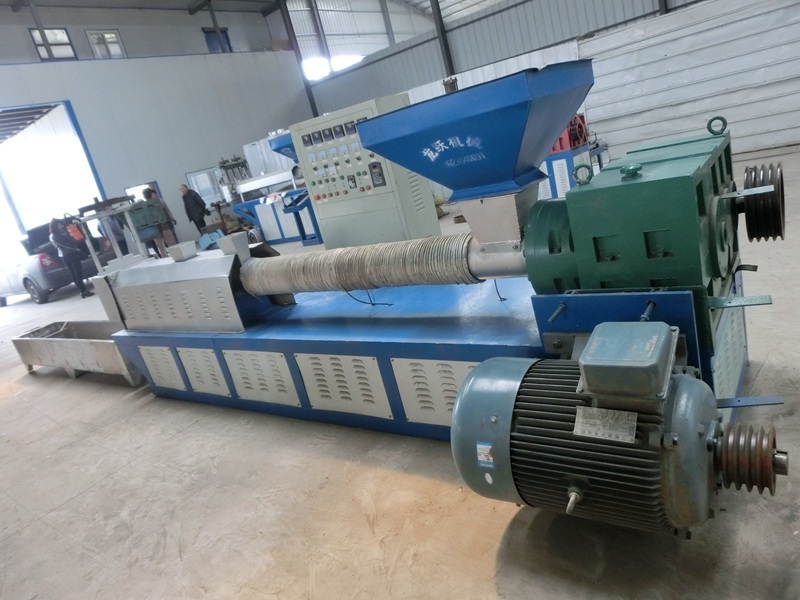

プラスチックペレット化装置 予熱器:
ケーブルの予熱は、絶縁体押出しとジャケット押出しの両方に必要です。絶縁層、特に薄い層の絶縁体においては、孔の存在を許可することはできず、コアは押出しの前に高温で予熱することによって、表面の水分や油を除去できます。シース押出しにおいては、その主な機能はコアを乾燥させ、湿気(またはクッションを取り囲む湿気)によるジャケット内の空隙の可能性を防ぐことです。予熱はまた、押出し中にプラスチックの内部圧力が急冷されるのを防ぎます。
プラスチックを押出す過程において、予熱を行うことで、冷たいワイヤーが高温の機械ヘッドに入る際に形成される温度差を解消でき、ダイ口でプラスチックと接触することで、プラスチックの温度の変動を避け、押出圧力の変動を引き起こすことを防ぎます。これにより、押出量と押出品質が安定します。
電気加熱コア予熱装置は押出ユニットで使用され、十分な能力と迅速な温度上昇が求められます。これにより、コアの予熱とコアの乾燥効率が高くなります。予熱温度はラインの速度によって制限され、一般的にはヘッドの温度に似ています。
プラスチックペレット化装置 冷却装置:
プラスチック押出し層が形成された後、機械のヘッドを出た直後に冷却して固化する必要があります。そうしないと、重力の作用で変形してしまいます。冷却方法は通常、水冷であり、水温に応じて急冷と徐冷に分かれます。急冷は冷水による直接冷却です。急冷はプラスチック押出しコーティングの成形に有利です。
しかし、結晶性高分子の場合、急速冷却のために押出層に残留内部応力が生じやすく、使用中に亀裂が発生することがあります。プラスチック層は急冷されます。ゆっくり冷却することで製品の内部応力を減少させます。冷却水槽には異なる温度の水を入れて、製品を徐々に冷却します。PEとPPの押出は、ゆっくり冷却され、つまり、熱水、温水、冷水を通じて行われます。三段階の冷却です。
廃プラスチックのリサイクルプロセスは:
リサイクル - 粉砕 - 洗浄 - 乾燥 - 顆粒化 - 押出成形(新製品)、顆粒化ラインはプラスチックリサイクルプロセスの重要な部分を占めています。
この組立ラインは何度もアップグレードされており、大量生産、低損失、低故障率、操作の簡便さ、低コストといった特長があります。造粒ラインはさまざまな加熱方法があり、顧客の電力容量とコストに応じて設計できます。また、顧客の材料や生産に応じて、質の高い合理的な組立ラインを提供します。