New development direction of waste plastic pellet making machine
Plastic recycling machines are mainly divided into three categories, namely injection molding machines, plastic pellet making machine, and blow molding machines. Plastic pellet making machine is a kind of plastic machinery. The high speed and high yield of the pellet machine enables investors to obtain larger output and high return with lower investment. However, the high speed of the screw speed of the pellet machine also brings a series of difficulties that need to be overcome: how to deal with the difficulties, that is, the direction in which the pellet machine will develop.
Process parameters such as melt pressure and temperature, body temperature, main screw and feed screw speed, and feed volume of the entire extrusion process are now widely used in modern developed pellet machines. The parameters of various raw materials, the current and voltage of the motor are measured online, and the closed-loop control of the microcomputer is adopted. Many companies have adopted online remote monitoring, diagnostics and control to network control the extrusion line. This is very beneficial for ensuring the stability of the process conditions and improving the accuracy of the product.
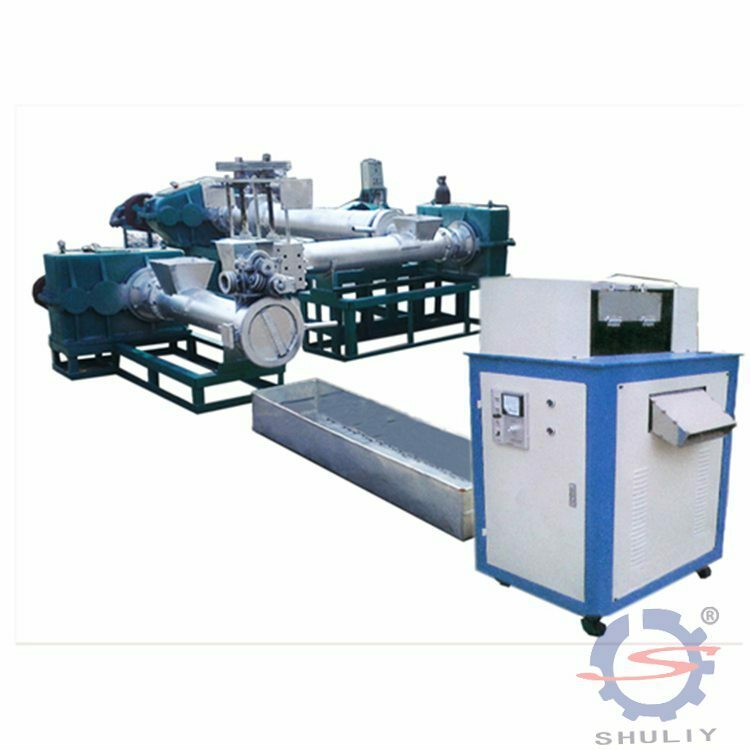
Intelligent and networked
High efficiency and multi-functionality of plastic pellet machine
The screw plastic pellet making machine is not only used for extrusion molding and mixing processing of polymer materials. The efficiency of plastic pellet making machine is mainly reflected in high output, low energy consumption and low manufacturing interest. Functional aspects. The use has been broadened into food, feed, electrodes, explosives, building materials, packaging, pulp, ceramics and other fields. In addition, a one-step extrusion process in which the mixing granulation and the extrusion molding process are combined into one is also worthy of attention.
Modularity and specialization of plastic pellet machines
Shorten the development cycle of new products, modular production can adapt to the special requirements of different users. Strive for a larger market share; and specialized production can arrange the production of various system module components of extrusion molding equipment and even global sales, which is very beneficial to ensure the quality of the whole period, reduce the cost, and accelerate the capital turnover.