Jinsi ya kudumisha mashine ya granulator ya povu ya EPS?
Takataka ya granulator ya povu ya EPS ni mashine kuu katika EPS povu granulating line. Granulator ya povu inachukua kuyeyuka kwa halijoto ya juu na kutoa povu na hutengenezwa kuwa CHEMBE baada ya mfululizo wa kuchora, kupoeza, na kukata. Katika mchakato huu, jambo muhimu zaidi kulipa kipaumbele ni inapokanzwa kwa mwenyeji.
Swali ambalo wateja wengi huuliza mara nyingi ni: mara ya kwanza unapoitumia, unahitaji tu joto kwa nusu saa; kwa nini mara ya pili unahitaji kuwasha moto kwa saa moja? Sababu ni nini?
Hii ni kwa sababu nyenzo zilizobaki kwenye skrubu hazikutoka baada ya siku ya kwanza ya uzalishaji, na kusababisha ndani kupoa na kuganda usiku kucha, kwa hivyo ilichukua muda mrefu wa joto kuyeyuka. Katika kesi hiyo, blowtorch inaweza kutumika kuharakisha kupanda kwa joto na kuifanya kuyeyuka haraka.
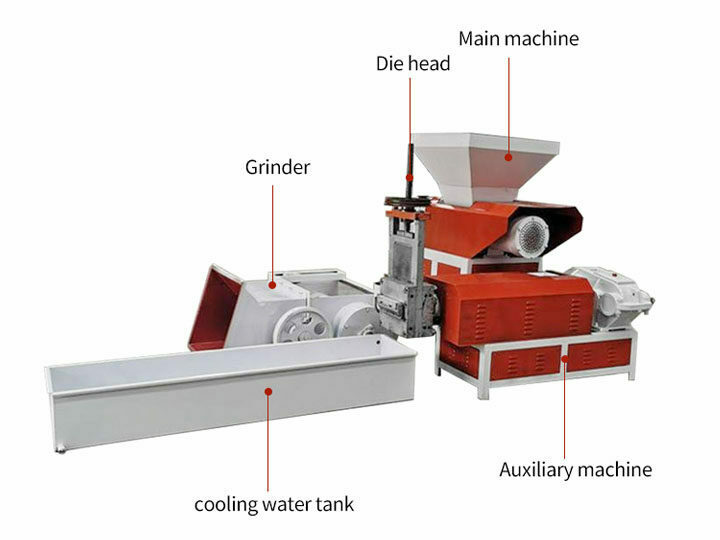
Kwa hiyo jambo muhimu zaidi ni kuweka nyenzo zinazotiririka safi kabla ya kuzima. Moja ni kuokoa muda, na nyingine ni kuokoa nishati.
Kwa kuongeza, ikiwa mashine haijayeyuka kabisa wakati mashine inapoanza, itaongeza kuvaa kwa screw. Katika hali mbaya, inaweza kusababisha uharibifu wa vipengele vya vifaa, na matokeo mabaya. Hii ndiyo sehemu muhimu zaidi ya kazi yetu ya matengenezo.
Kwa kuongeza, tunahitaji kuongeza mafuta kwa wakati na kusafisha sehemu mara kwa mara ili kuweka vifaa katika hali nzuri wakati wote ili kupata bidhaa bora zaidi.
Matengenezo ya muda mrefu ya Kipunje cha EPS
Mnamo Novemba, wateja kadhaa walitupigia simu ili kushauriana nasi: Vifaa vya kuchakata povu vya kuchakata chembechembe vilivyonunuliwa kutoka kwako hapo awali si rahisi sana kutumia kazini, na mzunguko hauwezi kunyumbulika kama hapo awali. Nifanye nini?
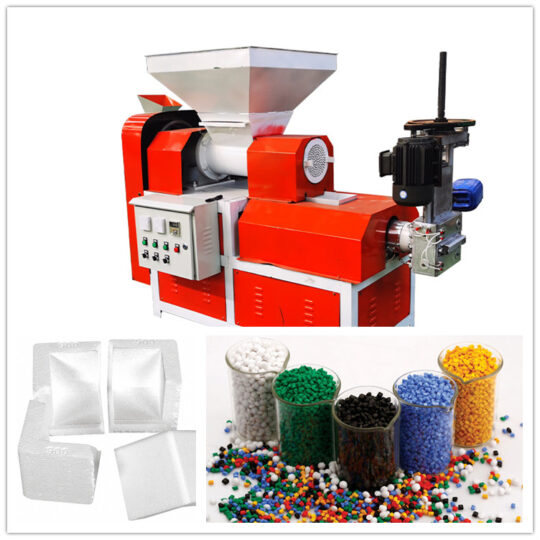
Sababu ya tatizo hili kwa kweli ni rahisi. Mashine haina mafuta au husababishwa na vumbi vingi kwenye chasi. Hapo chini, tutaanzisha ujuzi fulani wa matengenezo kuhusu granulator ya povu:
- Angalia hali ya kazi ya rollers mara moja kila baada ya miezi sita, safi fani juu ya rollers na mzunguko usiobadilika, kuongeza mafuta, na kuchukua nafasi ya fani zilizovaliwa au kuharibiwa kwa wakati.
- Kwa mpya iliyowekwa katika uzalishaji wa granulator ya kuchakata povu, baada ya muda wa kukimbia mtihani wa uzalishaji kufikia saa 500, sehemu zote za kulainisha zinapaswa kumwagika; kikombe cha mafuta, tanki la mafuta, bomba, na chujio vinapaswa kusafishwa, na kisha mafuta mapya yaliyochujwa yaongezwe.
- Angalia kuvaa kwa brashi ya motor DC mara moja kwa mwezi, kurekebisha nafasi ya kuwasiliana ya brashi na shimoni, badala ya brashi na mpya ikiwa ni lazima, na kusafisha shabiki kwenye motor wakati huo huo.
- Lubricator ya chanzo cha hewa mbili inapaswa kujazwa na mafuta ya turbine mara moja kwa mwezi, na unyevu kwenye chujio cha hewa unapaswa kuondolewa kwa wakati mmoja.
- Zoa vumbi na uchafu kwenye kisanduku cha kudhibiti umeme kila robo mwaka au nusu mwaka, angalia kiasi cha mafuta ya kulainisha kwenye tanki la mafuta na ujaze kiasi cha mafuta ya kulainisha kwa wakati.
- Safisha chujio cha hewa kwenye sanduku la gia kila robo au nusu ya mwaka, rekebisha mvutano wa ukanda wa V au mnyororo, angalia pete ya kuziba (pedi) kwenye mfumo wa nyumatiki, na ubadilishe sehemu zilizovaliwa inapohitajika.